Échangeurs thermiques à circuit imprimé
Les échangeurs thermiques à circuit imprimé Alfa Laval (PCHE) associent une robustesse et une intégrité supérieures à un taux de transfert de chaleur exceptionnellement élevé, dans une unité 85 % plus petite et plus légère que les échangeurs tubulaires comparables. Cette conception unique se traduit par d'excellentes performances, des coûts d'installation et de fonctionnement réduits, ainsi qu'une sécurité accrue. Chaque unité est également entièrement personnalisable selon vos besoins.
Efficacité exceptionnelle avec un encombrement minimal
- Construction entièrement en acier inoxydable, entièrement personnalisable en fonction du poste de travail et de l'application requise
- Conception robuste capable de supporter des pressions jusqu'à 1 000 bars (14 500 psi) et des températures de -196 °C (-320 °F) à 800 °C (1 472 °F)
- Permet des températures de pincement inférieures à 1 °C dans votre processus
- Immunité aux effets des pulsations de pression de fluide et des vibrations induites par l'écoulement de fluide
- Conforme au code ASME pour chaudières et appareils à pression (Section VIII, Division 1 avec certification U) et au marquage CE (PED 2014/68 / EU)
Printed Circuit Heat Exchangers - PCHE
Les échangeurs thermiques à circuit imprimé (PCHE) Alfa Laval constituent une solution ultra-compacte pour améliorer la durabilité dans les applications énergétiques, marine et pétrolières.
Les canaux de fluide gravés de manière photochimique offrent des performances thermiques exceptionnellement élevées, tandis que la liaison par diffusion à la fine pointe de la technologie produit un noyau solide garni d'une zone de transfert de chaleur. Le résultat combiné est une efficacité maximale et une empreinte minimale, garantissant le coût total du cycle de vie le plus bas.
Découvrez l'échangeur dédié à l'hydrogène comme carburant Hybloc.
Applications
Les échangeurs thermiques à circuit imprimé Alfa Laval sont spécialement conçus pour offrir une compacité et une efficacité inégalées dans des tâches propres et à haute pression, qui dépassent les capacités des autres échangeurs de chaleur à plaques soudées. La conception robuste peut gérer de manière fiable des pressions allant du vide à 1 000 barG (14 500 psiG).
Les applications marines typiques comprennent la vaporisation à haute pression dans les systèmes d’alimentation en gaz combustible, la regazéification du GNL sur les navires FSRU et SRV™. Dans le secteur de l'énergie, les échangeurs à circuit imprimé sont utilisés dans les applications de traitement du gaz et de GNL cryogénique.
Généralement, il s'agit de systèmes de compression de gaz en mer, de gaz d'hydrocarbures et de point de rosée dans l'eau. Dans le GNL, où une récupération d'énergie élevée est souhaitée, ils sont utilisés dans les systèmes de traitement des gaz à combustion instantanée et des BOG. On les trouve également dans les applications de préchauffage du gaz combustible de la turbine et du dioxyde de carbone supercritique (CO2) pour la production d'électricité.
Données techniques
Pression de conception
CE/PED Vide à 1 000 barG (14 500 psiG)
ASME Vide à 1 000 barG (14 500 psiG)
Température nominale
Acier inox 316 / 316L SST – 196 °C (cryogénique) à 800 °C (–321 °F à 1 472 °F)
Raccordements
Généralement 2 à 30 pouces, personnalisables
Matériaux standard
Acier inoxydable 316L SST (autres matériaux disponibles sur demande)
Dimensions/Poids :
Sur demande, sur mesure pour des besoins allant de quelques kilogrammes à plusieurs dizaines de tonnes
Fonctionnement
Principe de fonctionnement
Les échangeurs thermiques à circuit imprimé fonctionnent avec deux médias ou plus sur les côtés opposés d'une plaque assemblée par fusion. Il est possible d'avoir des flux haute pression des deux côtés et d'optimiser un motif de plaque 2D ou 3D pour fournir la longueur thermique et la perte de charge requises.
Conception
La conception de l'échangeur thermique à circuit imprimé présente un motif d'écoulement complexe gravé chimiquement sur des feuilles de matériau plates. Ce modèle d'écoulement est optimisé pour chaque tâche spécifique du client afin de fournir les caractéristiques thermiques et hydrauliques requises. Chaque configuration de plaque de circuit d'écoulement peut être différente, offrant ainsi la possibilité d'écoulements asymétriques et un comportement optimisé sur deux phases. Les plaques individuelles sont ensuite empilées dans un bloc et liées par diffusion dans un four ultramoderne à température et pression élevées. Plusieurs blocs peuvent être soudés ensemble pour créer la capacité thermique ou la zone de transfert de chaleur requise. Les collecteurs d'entrée et de sortie, les raccordements pour le client et (si nécessaire) les raccordements pour la vidange, la ventilation ou le nettoyage sont soudés sur le noyau terminé afin de finaliser l'échangeur thermique. Des pressions nominales pouvant atteindre 1 000 barG (14 500 psiG) dans un acier inox 316L sont réalisables avec cette configuration. Les surfaces de transfert thermique sont personnalisées en fonction des besoins.
Des caractéristiques uniques qui font la différence
Alfa Laval possède plus de 80 ans d'expérience dans la technologie de transfert de chaleur et nous développons en permanence de nouvelles innovations pour améliorer les performances, la fiabilité et l'impact durable de nos équipements. Nos échangeurs thermiques à circuit imprimé incluent un certain nombre de caractéristiques uniques que vous ne trouverez nulle part ailleurs :
OptiBond™
Une solution robuste et compacte pour les besoins de haute pression
La technologie de pointe de collage par diffusion offre la plus grande durabilité et efficacité thermique dans un échangeur thermique à plaques soudées ultra-compact.
3DPlate™
Empêche le colmatage par temps de gel
Un modèle de plaque 3D breveté maintient une efficacité élevée et une disponibilité maximale lors de l'utilisation de fluides à base d'eau tels que les glycols dans des applications cryogéniques.
Efficacité énergétique
Comment Alfa Laval peut optimiser votre efficacité énergétique ? Découvrez comment nos solutions permettent d'économiser 50 GW d'énergie par an et de réduire les émissions de CO2 d'au moins 25 millions de tonnes. Cela représente 550 fois l'empreinte carbone d'Alfa Laval.
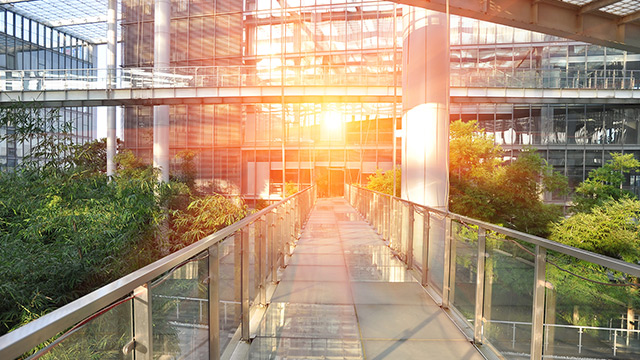