Réduire l'empreinte carbone du raffinage tout en améliorant ses résultats
L'intérêt pour les carburants renouvelables, notamment le Diesel renouvelable, continue de croître en raison des réglementations et de la pression sur l'industrie pour réduire la teneur en carbone des carburants. Alors que le marché propose des mesures d'incitation pour récompenser les investisseurs qui créent des sites à haute efficacité énergétique, la conception des processus traditionnels et les applications technologiques les freinent dans la poursuite cet objectif.
Quelle est la stratégie de réduction de l'intensité carbone ?
La stratégie de réduction de l'intensité carbone (IC) doit se concentrer sur la réduction de la quantité de gaz naturel, d'électricité et de produits chimiques requis dans la production de carburants renouvelables. Lors de la production de carburants renouvelables, il existe des moyens simples d'augmenter l'efficacité énergétique en raison de la nature hautement exothermique du processus. Un concepteur de processus peut utiliser cette énergie exothermique pour créer de la vapeur à haute pression afin d'assurer le chauffage du processus pour réduire les besoins en gaz naturel. Cependant, si l'objectif du projet est de créer un processus avec l'IC pratique la plus basse, cela ne suffira pas.
Alfa Laval a constaté qu'une quantité significative d'énergie de qualité inférieure est généralement perdue dans les installations pouvant réduire l'IC. Cependant, son intérêt est souvent limité lorsqu'une analyse énergétique traditionnelle de type coûts-avantages est utilisée. Nous avons également constaté que plusieurs bailleurs de licences de traitement impliqués pouvaient optimiser leur section de l'installation, mais la plupart du temps, personne ne se voit confier la responsabilité globale de l'intégration à l'échelle du site. Cela permet d'optimiser chaque partie de l'installation, mais le site global est sous-optimisé.
Vous trouverez ci-dessous une stratégie composée de trois étapes simples qui peut permettre à terme de réduire la quantité de gaz naturel/d'électricité nécessaire pour réduire l'intensité carbone du site.
Étape 1 : Maximiser le processus d'intégration thermique
Le propriétaire du projet doit porter l'objectif d'une IC réduite lors de la conception de l'ensemble du site. Les conceptions de processus proposées comprendront une intégration thermique basée sur la philosophie de conception des échangeurs thermiques traditionnels. Dans les premières réunions de projet, le propriétaire du projet devra communiquer les priorités aux bailleurs de licences de traitement pour le pré-traitement de l'alimentation ainsi que les processus liés à l'hydrogène et au Diesel renouvelable afin de réduire les dispositifs de refroidissement en maximisant l'intégration thermique.
La technologie d'échangeurs thermiques à plaques soudées permet de récupérer l'énergie avec des coûts différentiels qui n'étaient précédemment pas disponibles. Le propriétaire du projet doit rechercher toutes les possibilités de réduction de la quantité d'énergie nécessaire pour le gaz naturel ou l'électricité dans les fourneaux, les dispositifs de reformage, les compresseurs, les pompes, les colonnes de fractionnement, les tours réfrigérantes, les refroidisseurs d'air et les refroidisseurs d'eau de refroidissement.
Étape 2 : Créer des systèmes énergétiques
Le propriétaire du projet doit récupérer l'énergie résiduelle, devant à présent être retirée du processus, et trouver des méthodes pour la transférer dans des systèmes énergétiques. En utilisant les échangeurs thermiques à plaques soudées pour autoriser des approches rentables de températures proches, des systèmes énergétiques peuvent être créés avec la quantité maximale d'énergie extraite/introduite dans le processus. Les options à envisager comprennent :
- Vapeur à haute pression : Cette énergie extrêmement précieuse doit être utilisée lorsque l'impact maximal de réduction de l'intensité carbone est optimal. La plupart des clients envisagent des options de production d'électricité avec cette énergie.
- Vapeur à basse pression : Cette énergie peut être utilisée au sein du processus, ainsi qu'en dehors des limites des batteries (OSBL), pour générer la majeure partie de l'énergie nécessaire aux besoins de la production. On peut citer à titre d'exemple le chauffage dans le processus de prétraitement, les unités d'adoucissement d'eau et les systèmes à base d'amines.
- Boucles d'eau chaude : Les flux d'alimentation pour le Diesel renouvelable ont des difficultés à s'écouler à température ambiante, nécessitant de l'énergie pour réchauffer les réservoirs, les lignes de traitement et les systèmes de chargement/déchargement. Dans certains endroits, il peut également être intéressant de créer des systèmes de chauffage urbain pour utiliser cette énergie. Les boucles d'eau chaude sont une norme industrielle acceptée pour transférer la chaleur de qualité inférieure dans des lieux où elle est nécessaire tout en réduisant le refroidissement de l'installation.
Nous avons constaté un regain d'intérêt pour les systèmes mécaniques tels que le cycle organique de Rankine ou les refroidisseurs à adsorption pour utiliser cette chaleur résiduelle. Il a toujours été difficile de justifier ces processus, mais avec les nouveaux incitatifs économiques liés aux crédits carbone, ces options sont désormais rentables.
Étape 3 : Réduire le refroidissement de l'installation
Si ce système énergétique est conçu correctement, il n'y aura plus d'énergie pratique à récupérer, amenant les températures de sortie du processus à une plage comprise entre 150 et 160 oF.
La plupart des ingénieurs en conception de processus réduiraient le plus souvent la température du processus à 130 oF avec un refroidisseur d'air, nécessitant des dépenses en capital et de l'électricité. Le refroidissement final serait alors assuré par un échangeur thermique tubulaire, l'eau de refroidissement jouant le rôle de milieu liquide latéral. Ce processus consomme une grande quantité d'électricité et entraîne des coûts d'exploitation élevés en produits chimiques et en maintenance des échangeurs thermiques.
Les études Alfa Laval ont prouvé qu'à l'issue des deux premières étapes, le refroidissement final de la troisième étape peut être effectué avec un système en circuit fermé qui associe la technologie à plaques soudées et le refroidisseur Niagara Wet Surface Air Cooler. Le projet bénéficie ainsi d'un double avantage :
- Élimination des dépenses d'investissement qui seraient habituellement consacrées aux refroidisseurs d'air et aux systèmes de prétraitement d'eau.
- Réduction des dépenses d'exploitation qui sont habituellement consacrées au traitement de l'eau douce. Cela réduit de 60 % la consommation globale d'électricité et les ajouts de produits chimiques dans l'eau de refroidissement.
Enfin, l'utilisation de la technologie d'échangeurs thermiques à plaques soudées, associée à une stratégie agressive de réduction de l'intensité carbone, permettra à nos clients de réaliser des investissements supplémentaires et d'obtenir des rendements qui réduiront l'intensité carbone et favoriseront un avenir durable tout en améliorant leurs résultats financiers.
À propos de l'auteur
Mike Buettner
Technologue spécialisé en plaques soudées pour les raffineries, Mike Buettner met en œuvre la technologie des échangeurs thermiques dans des raffineries aux États-Unis. Mike travaille depuis plus de 25 ans dans l'industrie du raffinage, aux États-Unis et en Asie, à différents postes au sein de prestataires en performances énergétiques, de raffineries et de fournisseurs de solutions technologiques. Mike est titulaire d'un diplôme en génie chimique de l'université technologique du Michigan ainsi que d'un MBA (Master in Business Administration) de l'université du Minnesota.
Consulter le webinaire Intensité carbone
Nos experts en raffinage proposent des informations issues d'études de cas pour réduire l'intensité carbone et atteindre les objectifs de durabilité avec les échangeurs thermiques à plaques soudées Alfa Laval.
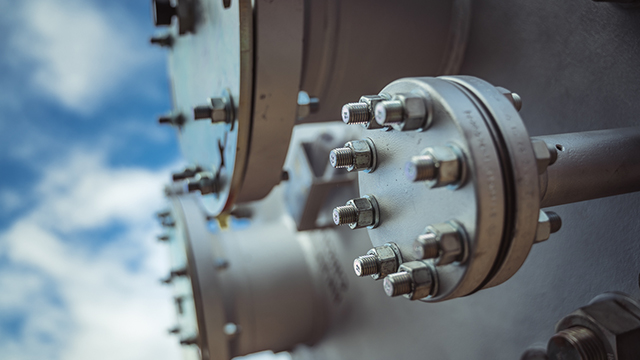